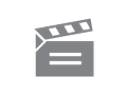
Description
The programme, filmed at Ashton and Moore Ltd., and at Ionic Plating Co., examines methods by which artefacts are finished using techniques such as spray painting, electroplating, polishing, anodis...ing, etc.
The programme, filmed at Ashton and Moore Ltd., and at Ionic Plating Co., examines methods by which artefacts are finished using techniques such as spray painting, electroplating, polishing, anodis...ing, etc.
Module code and title: | T352, Materials processing |
---|---|
Item code: | T352; 15 |
First transmission date: | 25-09-1979 |
Published: | 1979 |
Rights Statement: | |
Restrictions on use: | |
Duration: | 00:25:00 |
+ Show more... | |
Producer: | Colin Robinson |
Contributors: | Michael Ashton; Ken Reynolds |
Publisher: | BBC Open University |
Keyword(s): | Anodising; Cathode; Electrolysis; Electrolyte; Electroplate; Fasteners; Industry; Polishing; Screws, nuts and bolts; Spraying |
Footage description: | Opening comments from the three contributors introduce the programme. Shots of aerosol spray caps after anodising and dyeing. Ken Reynolds at the Ashton and Moore factory briefly outlines the three basic reasons underying finishing operations. He then goes on to list some examples of the first two reasons, decoration and protection of the article. Reynolds shows several examples of decorated articles - jewellery, lampshades, bathroom fittings, etc. He uses an animated diagram to illustrate the protective chrome layer on a car bumper. Reynolds holds up a small hydraulic ram and a poppet valve from a car while he discusses the third reason for finishing artefacts - to impart specific engineering properties such as anti-corrosion surfaces, etc. Over film shots of the paint shop at Ashton and Moore, Reynolds briefly describes one simple method of finishing, that of spray painting. Ken Reynolds and Michael Ashton examine an unfinished brass and copper goblet and discuss how an article might be finished by electropolishing. Film shots of the process and also an animated diagram illustrate their points. Reynolds and Ashton go on to discuss the anodising process, a process for finishing aluminium products. Film shots of the anodising baths while they talk. Ken Reynolds and Michael Ashton next discuss the problems involved in silverplating a goblet. Ashton demonstrates a special jig which was designed to hold artefacts like the goblet during electroplating. He goes on to explain how he would go about electroplating a complex shape such as a beer keg valve. Barrel plating, a process by which large quantities of small objects can be electroplated, is explained by Ken Reynolds. Film shots show the process while he talks. Reynolds goes on to discuss duality control in electroplating. Shots of a test being conducted which checks the thickness of the metal deposits. He follows this with a discussion on selective electroplating of artefacts and how this is achieved. Peter White explains the electoless nickel process by which nickel is applied to a surface with no electric current being involved. He points out that this is a particularly useful process for applying uniform coatings of nickel to complex shapes. He holds up some articles which were treated by this method and describes the superior wear and anti-corrosion characteristics which the process gives to the product. White and Reynolds discuss the application of the electroless nickel process to the production of moulds used for manufacturing plastic articles. Reynolds and Ashton return to discussing barrel plating particularly its limitations. Reynolds sums up the programme. |
Master spool number: | 6HT/72837 |
Production number: | 00525_5339 |
Videofinder number: | 1442 |
Available to public: | no |